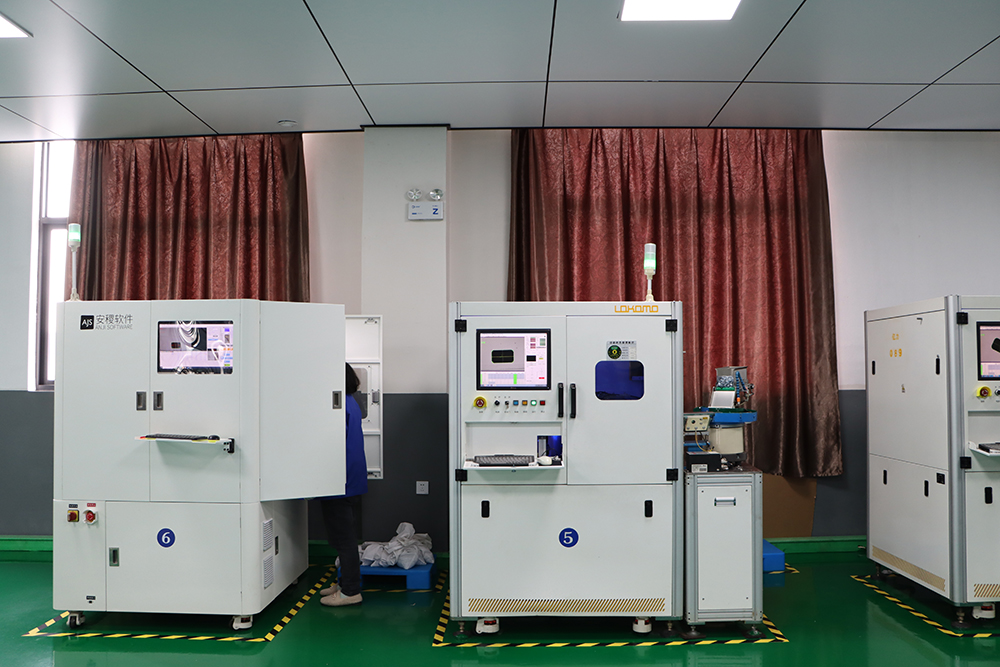
In today's fast-paced manufacturing industry, ensuring the quality of products has become more critical than ever before. One crucial aspect of maintaining high product quality is the inspection process. Traditionally, manual inspection methods were employed, which were often time-consuming and prone to human error. However, with the advancement in technology, the introduction of automatic visual sorting machines has revolutionized the inspection process, enabling more scientific and effective inspection of product quality.
One of the significant advantages of automatic visual sorting machines is their ability to detect and sort magnets accurately. Magnets , especially neodymium magnets , are widely used in various industries due to their exceptional magnetic properties. These magnets are made from a combination of neodymium, iron, and boron, making them incredibly powerful. However, the manufacturing process of these magnets requires strict tolerances to ensure their quality and performance.
The tolerance of magnets refers to the acceptable variations in dimensions and magnetic properties within a specified range. Any deviation from these tolerances can result in magnets that are substandard or do not meet the required specifications. Manual inspection methods often struggle to identify these minute variations accurately. However, automatic visual sorting machines utilize advanced imaging technology and algorithms to precisely analyze the dimensions, magnetic properties, and overall quality of every magnet, ensuring that only magnets within the specified tolerance range are approved.
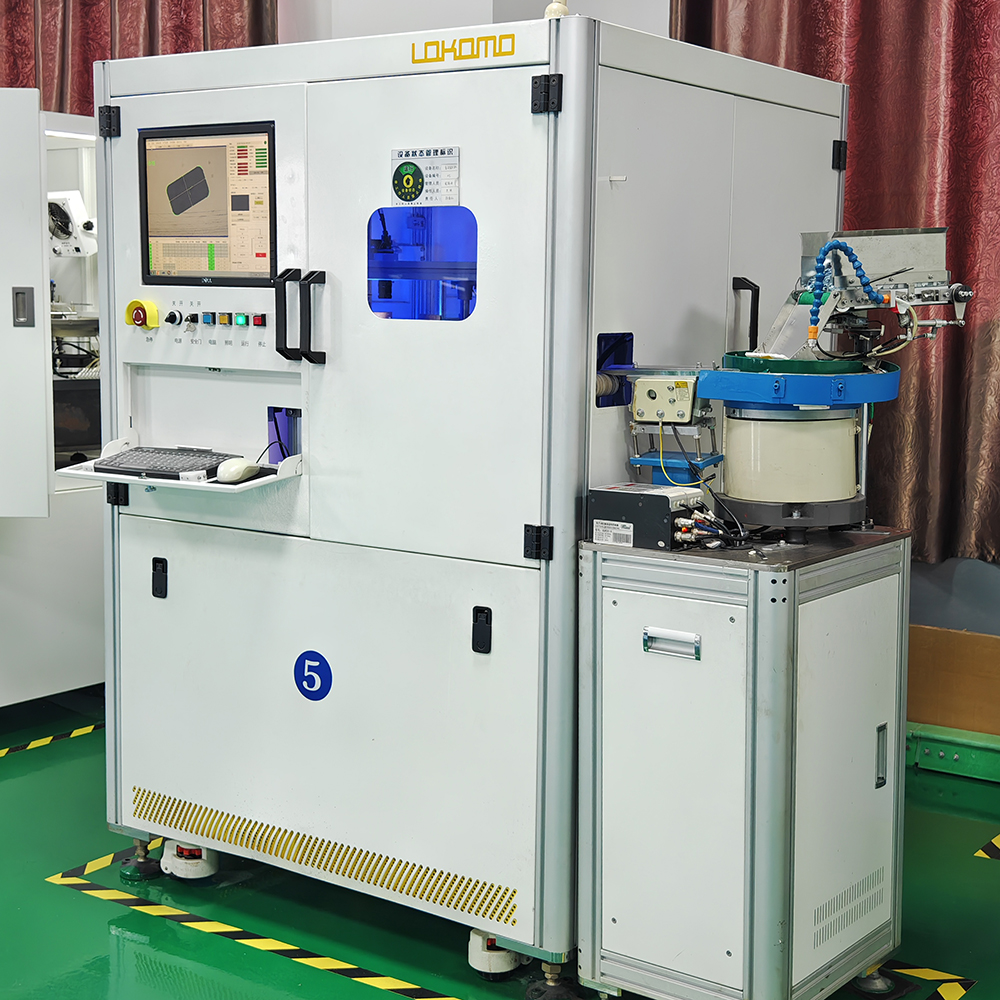
The visual inspection process starts with the automated feeding of magnets into the sorting machine. The magnets are then systematically analyzed using high-resolution cameras, which capture detailed images of each magnet from multiple angles. The images are processed by computer algorithms, which analyze various characteristics, such as size, shape, magnetic field strength, and surface defects. These algorithms are designed to detect even the slightest variations in these characteristics against the predetermined tolerance range.
Once the analysis is complete, the automatic visual sorting machine sorts the magnets into different categories based on their quality. Any magnets that fall outside the acceptable tolerance range are rejected, while those within the range are carefully collected and set aside for further processing or packaging. By automating this process, manufacturers can significantly reduce the time and effort required to inspect and sort magnets accurately, thus improving production efficiency and reducing the risk of defective products reaching the market.
Moreover, automatic visual sorting machines offer several additional benefits. Firstly, they eliminate the subjective nature of manual inspections, providing consistent and objective evaluations of product quality. Secondly, the machines can operate 24/7, ensuring continuous inspection and sorting without any human fatigue or errors. Lastly, the inspection results are recorded digitally, allowing manufacturers to analyze and monitor trends in product quality over time, facilitating better overall process control and optimization.
Post time: Nov-17-2023